工程間の情報を連携させ、
業務全体の効率化を実現。
- 自動車関連
- 見える化
- 在庫管理
- 工程管理
- トレーサビリティ
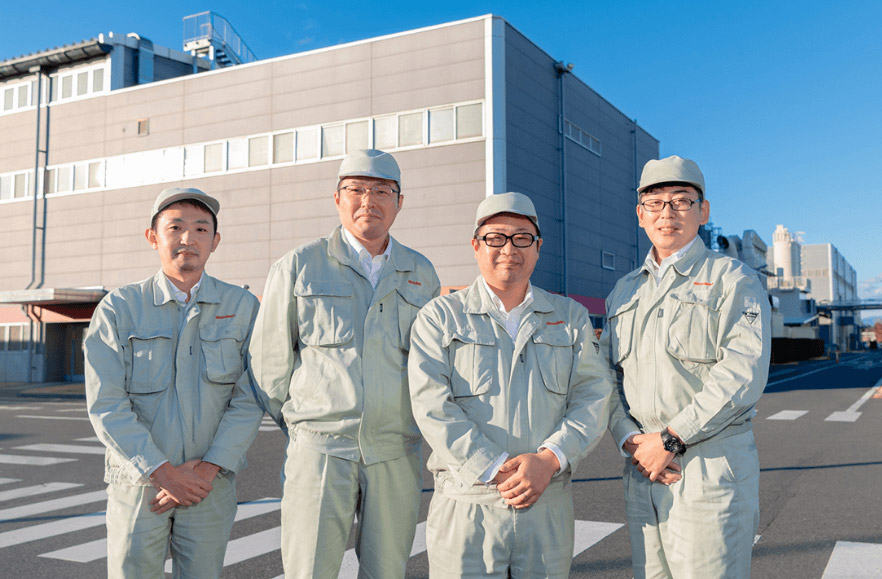
日清紡ブレーキ株式会社 様
- 設立:
- 2009年4月1日
- 資本金:
- 9447.4百万円
- 業種:
- 製造業
- 事業内容:
- 自動車、輸送用機械器具用摩擦材およびその部品の開発、製造、加工、売買および輸出入
- 従業員数:
- 717名(2020年12月末 嘱託含む)
日清紡ブレーキ様は、自動車や輸送用機械器具のブレーキ製品を製造しています。今回は、館林事業所生産技術部の皆様に、TONOPS®導入の経緯や使用時の感想、得られた成果について伺いました。
課題
- 工程ごとに点在するシステム
- 人手によるデータ入力・連携
- 煩雑なトレーサビリティ業務
- 在庫把握・棚卸業務の負荷
TONOPS®の導入
- 工程間のデータ連携・一元化
- データ手入力の廃止・削減
- テスト運用含む計画的な導入
成果
- 正確かつリアルタイムな情報管理
- データ連携による入力負荷低減
- 迅速なトレーサビリティ対応
- 在庫管理業務の負荷低減
事業について
ブレーキに用いる摩擦材を、世界中の自動車・輸送機器に提供しています。
私たち日清紡ブレーキは、自動車や輸送用機械器具のブレーキなどに使用される摩擦材を製造しています。主力製品であるディスクパッドやブレーキライニングなどの摩擦材は、人の命に関わる部品であり、厳格な品質要求に応えることで世界トップクラスのシェアを獲得しています。館林事業所は、世界に複数ある生産拠点のなかでもアジアの中核工場として、主要製品の生産を行っています。
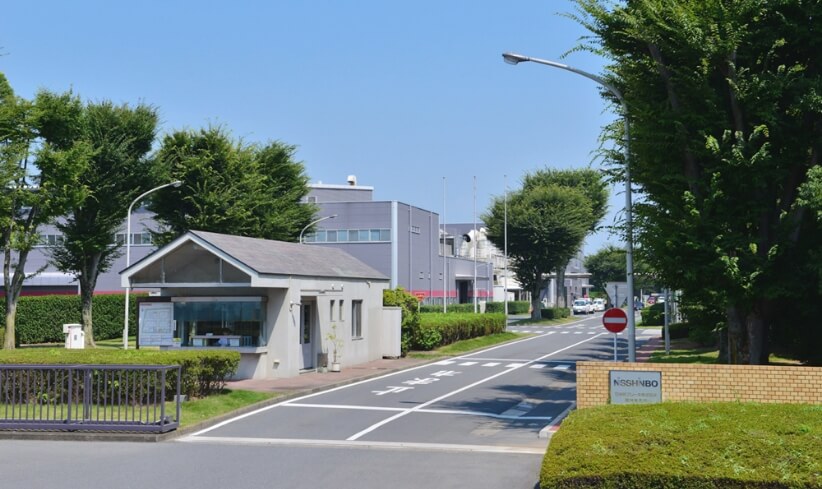
当時の課題感
工程ごとにシステムが異なり、情報管理が現場の大きな負担になっていました。
TONOPS®導入以前は、以下が課題でした。
(1)工程ごとに独立したシステムの存在
工程ごとに異なるシステムが存在していたため、情報管理に手間と工数がかかっていました。
品質データを取得する際には、各工程のシステムを確認する必要がありました。
(2)紙ベースの品質記録
2000種類ある品番それぞれの検査項目に従い検査し、結果を紙に記載したうえでExcelへ入力 する必要がありました。
(3)在庫管理業務の負荷
月末の棚卸作業では、各工程の仕掛品在庫状況を人手でカウントする必要がありました。
カウント結果を二重、三重に確認することで正確性を担保していました。
当時の現場は人手作業が多く、負担を軽減するためにも、システムの一元化が必要だと考えました。
システム導入の経緯と
TONOPS®を選んだ理由
「過去の実績」と「生産工程に適したシステム提案」から導入を決めました。
日清紡ブレーキでは、2014年にシステムの再構築に着手し、開発を担うベンダーの選定を行いました。当時、事業所内の各工程を担当する複数のベンダーが候補として挙がっていました。東レエンジニアリング(現・東レエンジニアリングDソリューションズ)とは、1990年代のアメリカ工場と中国工場の設立時に、プラント工事・設備機器の立上げから生産管理システムの導入まで、ワンストップで依頼した経緯がありました。また導入後も、変更や改修が必要になれば手厚くサポートしていただきました。こうした実績から、設備とシステムが一体となった仕組みを構築していただけるのではないかと考えました。そこでお問い合わせしたところ、日清紡ブレーキの製造工程を理解したうえで、運用に適したシステムをご提案いただきました。同社が手掛けるTONOPS®なら、現場の運用に適したシステムを構築できるに違いない。そのような考えから、システム導入を依頼しました。
導入の成果
工程間の情報連携により、品質確保と業務効率化を両立できました。
TONOPS®の導入後は、工程間の情報連携が実現し、さまざまな面で業務効率化へとつなげることができました。例えば、品質データの取得は、従来なら各システムを確認しながら半日がかりで行っていた作業ですが、TONOPS®ではシステム上で検索することができるようになりました。
現場では、在庫管理にハンディターミナルと二次元コードを使い、現物の動きをリアルタイムに把握できる仕組みを構築したことで、棚卸業務における工数を月次単位で1人分削減することができました。また、BIツールを使うことにより、製造実績や各工程の稼働状況を見える化しています。計画に達していない品目がある場合、どの工程で問題が発生しているかわかるため、スピーディーに対策を検討できるようになりました。検査工程では、作業者の端末で検査指示が確認できることに加え、測定器のデータが自動で取り込まれるようになり、入力ミスの削減にも貢献しています。
このように、さまざまな業務で必要な工数を踏み品質を確保しながら業務効率化できたことは大きな成果でした。
導入による成果
- 工程間の情報連携により、各種データを共有し作業を効率化
- 製造実績に品質データが紐付き、トレーサビリティがさらに向上
- デジタル化による在庫管理・棚卸作業の効率化
- BIツールの活用でライン状況を見える化し、効果的な工程改善を実現
- 検査項目のマスタ化で、システムから次の検査指示を取得・作業
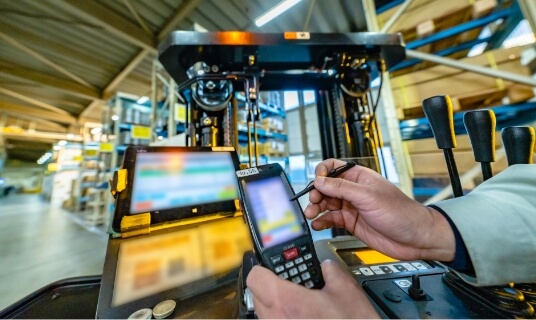
在庫搬出の現場では、作業者のハンディターミナルに品名・数量・格納位置・移動場所などの情報を伝達する。
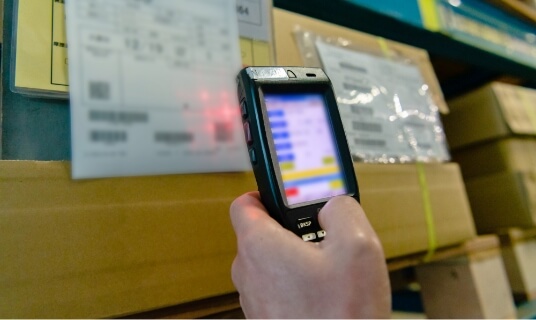
二次元コードを読み取ることで、正しい品目かをチェック。在庫移動もシステム上で把握できる。
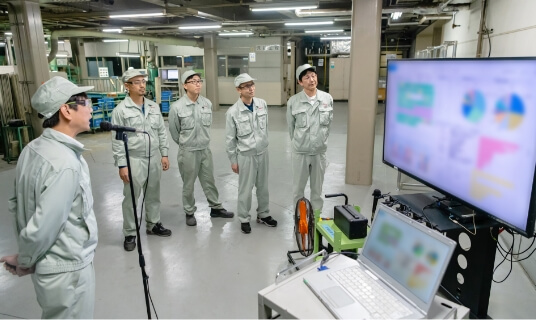
製造実績やラインの稼働状況を朝礼時に共有し、課題や対策をすりあわせたうえで業務に臨む。
導入時に
苦心されたこと
製造現場からの数々の要望に、どう対応するか。整理しシステムに落とし込むのが大変でした。
システムの導入・変更は、現場のオペレーションを大きく変えます。そのため、実際の運用に適したシステムを構築する必要がありますが、現場からの要望が多くどのように整理して反映していけばいいのか悩みました。そこでエンジニアの方に相談したところ、要望をシステムイメージにわかりやすく落とし込んでくれ、それをもとに現場とスムーズに協議することができました。また、作業工程の指図書を表示するタブレット画面の設計では、ボタンの色や配置、文字の大きさなど、現場からさまざまな要望や意見が出ました。それらを一つ一つ確認しながらテスト画面に落とし込んでもらえたことで、最終的に現場の納得感が高いシステムに仕上がりました。
システム導入後も、重要な機能の改造や追加がある場合は、プロトタイプによる運用と現場ヒアリング、改善という対応をいただいています。現場でのスムーズな運用のために必要な手立てを講じてくださるので、大変助かっています。
今後の展望
自動で計画立案する「提案型」のシステムへと進化させ、よりよい生産活動を実現したいです。
今後は生産管理システムを活用してエネルギーの見える化を行い、省エネ対策につなげることで社会貢献を目指しています。製造現場における省エネ対策への取り組みは、脱炭素社会の実現をはじめとするエネルギー危機対策として重要なテーマだからです。
また、生産管理システムには現在、製品マスタに紐付き2000種類に及ぶ製品の製造実績のデータが蓄積されています。日清紡ブレーキが将来的に目指すのは、蓄積したデータと外部データを分析することで、「いつ・なにを・どのように生産するか」を自動で計画立案する「提案型」の生産管理システムです。人のカン・コツに頼らず、作業の平準化を図るために、よりいっそうシステムを進化させていきたいと考えています。東レエンジニアリングDソリューションズでは、AIを活用した需要予測や障害予測の機能開発に取り組んでいると聞いています。こうした最新機能の提案に、今後も期待しています。
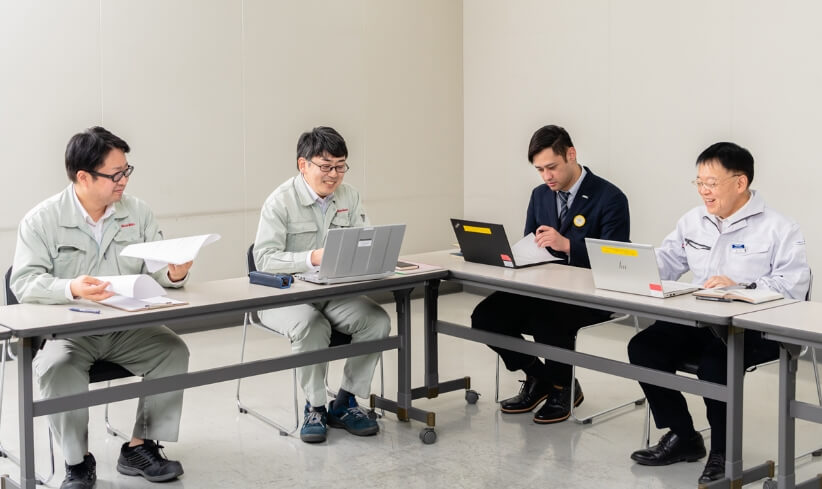